Runway Light Can Stabilization at Major Mid-Atlantic Airport
Problem
At a busy Mid-Atlantic hub airport, administrators knew they had a problem when runway center line light cans settled to a degree that required the use of the highest available light can extensions. As the proper function of the lights depended on precise installation and orientation, they knew that additional settlement would compromise the safety and reliability of the airport. The airport reached out to consulting engineers, who under a maintenance contract brought in URETEK to see if it was possible to design a solution involving URETEK Deep Injection® (UDI).
Analysis
A solution needed to be found to stop the cans from continuing to settle. The traditional remedy involved removing the light can assembly, digging out the area around the cans, re-compacting the foundation soils, reinstalling the cans, and rebuilding the runway around each work area. Because this repair method would close the runway to daytime operations, airport officials were hoping for a less-intrusive option through UDI. Soils reports and construction drawings were provided to URETEK’s engineering department, along with the results of the consulting engineer’s Heavy Weight Deflectometer (HWD) testing conducted at the site. Based on a review of all available data, URETEK formulated a site-specific injection plan for the runway.
Solution
Technically, this was a very challenging project. Each of the runway lights had a narrow azimuth and elevation light beam that was not to be disturbed. As such, URETEK needed to increase the load bearing capacity of the foundation and base soils beneath and around the lights without appreciably lifting the lights. Precision injection was called for, and URETEK crews drew upon decades of experience with airport runway jobs when completing this project.
Result
URETEK successfully completed this project in only four short work nights. Each night during the project, the runway was closed at 10 p.m., the electrical system was locked down and tagged out, the subject lights were removed from the light cans, and the subject cans were drained. URETEK crewmembers began work at midnight with the understanding that they had to be off the runway by five a.m. so the runway could be made active by six a.m. Under these conditions, the crew was able to stabilize four to five light cans each night. The airport Operations Manager was very impressed with how non-invasive and clean UDI proved to be. Expecting to have to clean the work area before resuming airport traffic, he was thrilled to note that URETEK crewmembers left the work area each morning cleaner than they found it. He reported that the only way he could tell that URETEK had worked on a can was by the color of the epoxy used to plug the 7/8″ injection holes. Finally, as a testament to the reliability of UDI, follow-up HWD testing was conducted at the runway work site every six months for three years after the project was completed, with no detectable settlement recorded.
URETEK Deep Injection® (UDI)
Widely referenced throughout our industry, UDI involves the injection of structural polymer into base and subgrade soils to increase the load bearing capacity. This is achieved by injecting the polymer through small holes drilled directly through the pavement structure to depths determined by site-specific analysis. Our URETEK 486 Star® material flows easily into voids and weak zones within the soil mass below. Through a controlled chemical reaction, the expanding polymer compacts surrounding soils and applies a controlled pressure on targeted areas of the affected pavement above. If needed, a multi-injection design plan is utilized to gently return the pavement to its original grade. The composite material quickly cures into a strong, dimensionally stable, and water-resistant geo-material, providing years of reliable service.
URETEK 486 Star®
URETEK 486 Star® polymer is a two-component, high-density, expanding thermoset polyurethane system. It was developed to be the ideal solution for under-sealing, void filling, lifting of settled pavement, stabilization and stiffening of weak soils, and for encapsulating and sealing buried infrastructure. URETEK 486 Star® is environmentally inert, non-toxic, and resists underground water erosion or weakening due to its industry-leading hydrophobic properties.
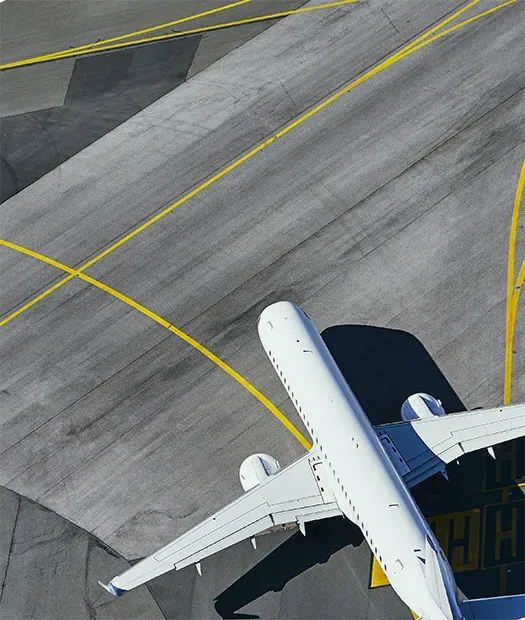
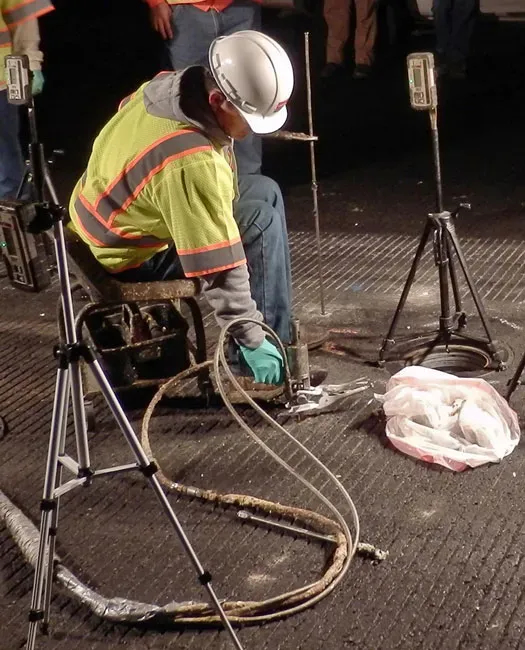
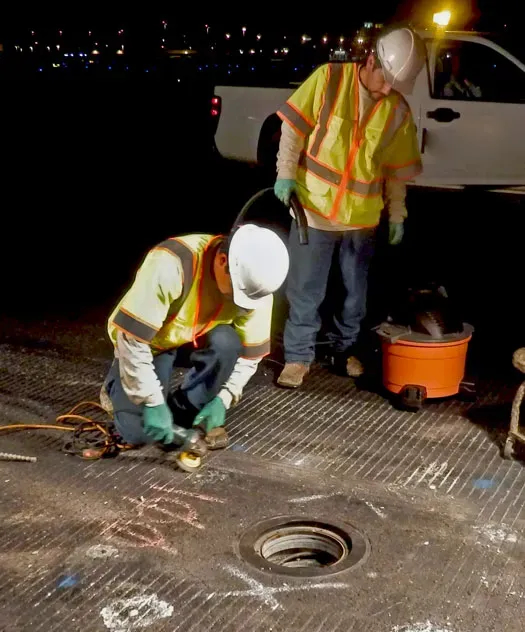