COUNTERSINKING INJECTION SYSTEM
IT'S NEVER BEEN EASIER TO MILL THE ASPHALT OF REHABILITATED ROADS
A commonly voiced concern with polymer injection is the residual thin-walled steel tubes left in the pavement, which affect the ability to mill and thus recycle asphalt. Typical repair methods clear these tubes at the tail end of their processes, often undermining the improvements to shear strength they had gained. Now, the patented countersinking injection tube system included in the URETEK Deep Injection® (UDI) process avoids the common pitfalls of removing such tubing.
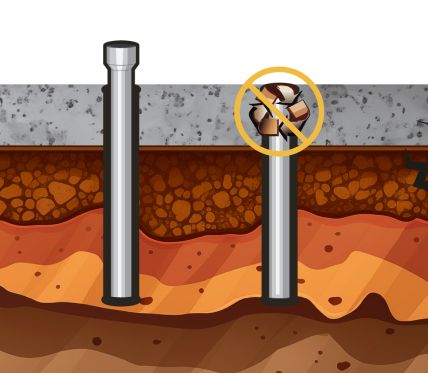
CUTTING TUBES AFTER INJECTION
This leaves the tubes at or just below grade, causing milling machine blades to cut into the steel tubing and preventing asphalt recycling due to contaminants.
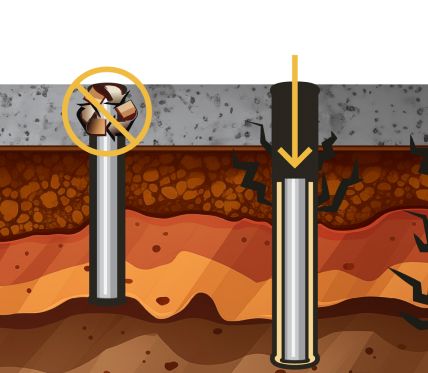
DRIVING TUBES DEEPER POST-INJECTION
Vibrating tubes to sink them deeper can break newly formed bonds in the soil’s geopolymer matrix, as can driving tubes down more directly.
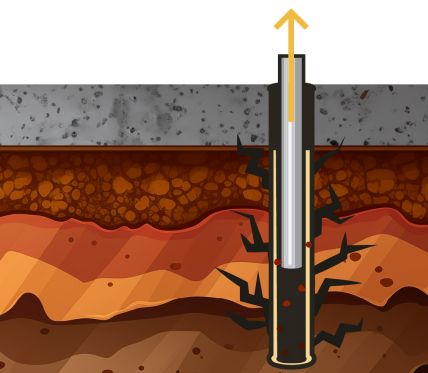
REMOVING TUBES AFTER INJECTION
Removing steel tubes removes a structural element of the soil, leading to problems like moisture infiltration, sloughing, and weak soil layer reformation as untreated or loose soils fill the void space.
WITH UDI®, URETEK PRESERVES BONDS THAT OTHERS DESTROY
A repaired soil system's strength relies in part on shear strength gained from newly formed bonds between the injection tubes and the soil’s geopolymer matrix. As part of its industry-leading URETEK Deep Injection® (UDI) Process, URETEK uses specialized tools to countersink all tubing before proceeding with polymer injection, preserving critical links in the structure of a foundation. We engineer our injection patterns precisely to maintain complete volumetric control, guaranteeing a minimal Factor-of-Safety (FOS) and preventing overuse.
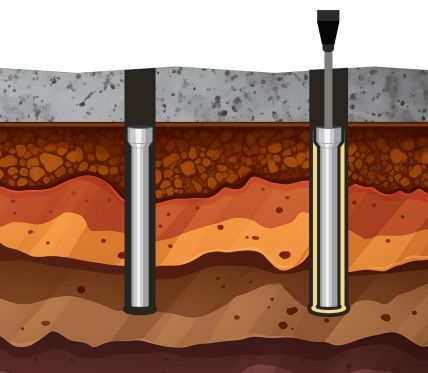
STEP 1
UDI® Process begins with tube pre-driven 6” below surface
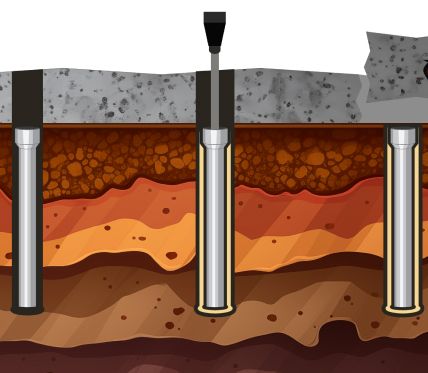
STEP 2
URETEK 486 Star® polymer is easily injected at depth
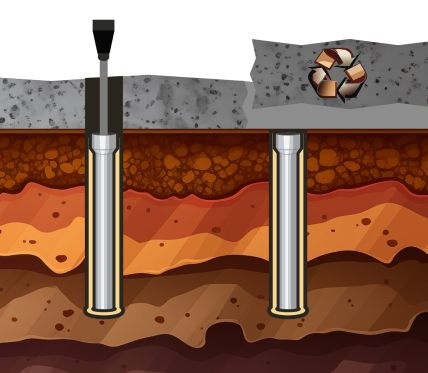
STEP 3
Tube remains in while asphalt recycled
THE BENEFITS OF COUNTERSINKING YOUR TUBES
NO CUTTING/VIBRATING
Tubes stay structurally sound with no post-injection cutting or vibrating needed.
NO TUBE REMOVAL AFTER INJECTIONS
Tubes remain in place, preventing void space in the geopolymer matrix.
GREEN SOLUTION
An eco-friendlier way for polymer injection that supports contamination-free asphalt recycling.
NO SHIFT LIMITATIONS
Project advancement is unrestricted, with no protrusions or limitations between shifts.
NO PUNCTURE RISK
Traffic control removal between shifts ensures no risk of punctured tires or lost tubes.
NO SAFETY RISK
No exposed tubing hazards like slips, trips, falls, or impalements overnight or between shifts.
ABOUT URETEK
URETEK is a pioneer in Polymer Injection technology, leading the industry in research, development, and application for over 30 years. We adopt specialized tooling, procedures, and processes to ensure successful, cost-effective pavement, soil, and infrastructure projects. We're so confident in our capabilities that we offer a two-year warranty on Public Works and Federal projects and cover any costs that incur should a crew heave your asphalt pavement during Public Works, Streets and Maintenance, or Roadways, Freeways, and Highways projects.
DEEP EXPERTISE
When you work with URETEK, you get the highest-quality, most widely reference soil stabilization solution in the industry—all from the engineers who invented it.
BOUNDLESS ENTHUSIASM
Thousands of successful projects have taught us there’s always more to understand than what’s apparent on the surface. Let’s dig in.
COMMITMENT TO SAFETY
From first deployment to final cleanup of your worksite, we prioritize safety and lack of disruption in everything we do.
A URETEK EXPERT IS READY TO DIG INTO YOUR PROJECT
Contact us for more information about URETEK, countersinking injection system, or anything else you'd like answers to.
CONTACT US