Runway Repair at Lackland Air Force Base
Problem
The 433rd Air Wing is an Air Force Reserve unit that operates the C-5 Galaxy out of its home at Lackland Air Force Base in Texas. Representatives from URETEK and the 802nd Civil Engineering Squadron performed a site visit to problem areas on the 433rd Air Wing (AW) Apron. The 802nd representatives identified three problem areas to URETEK personnel:
- Problem Area 1 – faulted slabs near the intersection of Taxiway H and the 433 AW Apron,
- Problem Area 2 – prematurely cracked slabs on and near the apron taxilane extending from Taxiway H, and
- Problem Area 3 – pumping slabs near the Entry Control Point where the apron taxilane extending from Taxiway H ends.
Analysis
A URETEK crew was deployed to Lackland to gather additional information on the three problem areas by performing Dynamic Cone Penetrometer (DCP) tests, mapping pavement distresses, and collecting slab elevation data.
The following considerations were applied to proposals for lifting faulted pavement and performing in-situ stabilization of soils beneath the pavement:
- minimizing disruption to 433rd AW operations during the project,
- accommodating future slab replacement projects (e.g., stabilization of foundation soils should withstand removal of current slabs and construction of new slabs), and
- reducing foreign object damage potential.
Solution
URETEK’s solution involved the URETEK Deep Injection® (UDI) process. One UDI depth was used in Problem Area 1, and two injection depths were used in Problem Areas 2 and 3. Foreign object damage potential was minimized by capping injection holes with rapid set epoxy and by buffing caps for a smooth pavement surface.
Result
URETEK realigned the 14 faulted slabs in Problem Area 1, stabilized the soils ten feet down (measured from the surface) for 54 slabs in Problem Area 2, and displaced the water and stabilized the soils under 26 slabs in Problem Area 3. URETEK successfully addressed these three problem areas at Lackland Air Force Base in just 26 weekdays with very minimal mission disruption. In addition to reopening the apron every night for use by the 433rd AW, URETEK maintained a small footprint during repair operations and cleaned the repair area after each day’s work. URETEK also made sure to think beyond the immediate fix and accommodate future slab replacement projects by countersinking injection tubes beneath the bottom of the pavement.
URETEK Deep Injection® (UDI)
Widely referenced throughout our industry, UDI involves the injection of structural polymer into base and subgrade soils to increase the load bearing capacity. This is achieved by injecting the polymer through small holes drilled directly through the pavement structure to depths determined by site-specific analysis. Our URETEK 486 Star® material flows easily into voids and weak zones within the soil mass below. Through a controlled chemical reaction, the expanding polymer compacts surrounding soils and applies a controlled pressure on targeted areas of the affected pavement above. If needed, a multi-injection design plan is utilized to gently return the pavement to its original grade. The composite material quickly cures into a strong, dimensionally stable, and water-resistant geo-material, providing years of reliable service.
URETEK 486 Star®
URETEK 486 Star® polymer is a two-component, high-density, expanding thermoset polyurethane system. It was developed to be the ideal solution for under-sealing, void filling, lifting of settled pavement, stabilization and stiffening of weak soils, and for encapsulating and sealing buried infrastructure. URETEK 486 Star® is environmentally inert, non-toxic, and resists underground water erosion or weakening due to its industry-leading hydrophobic properties.
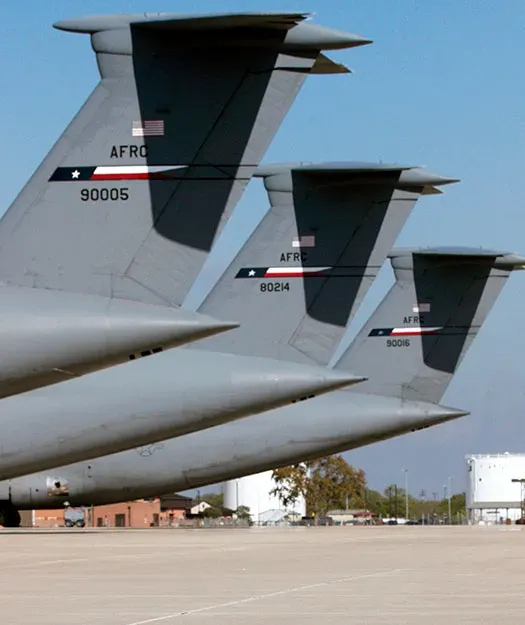
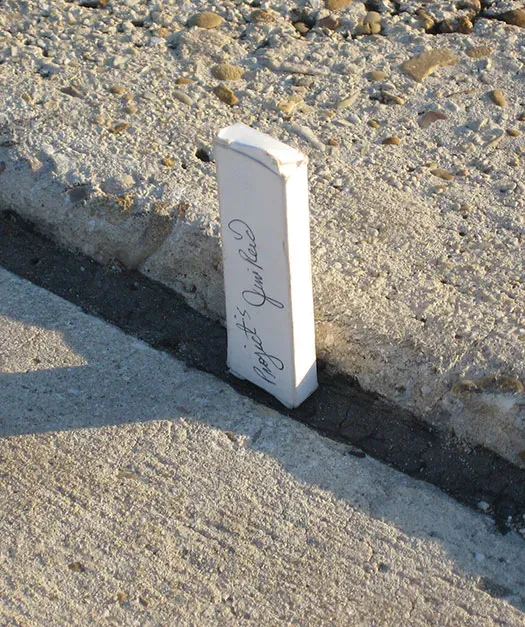
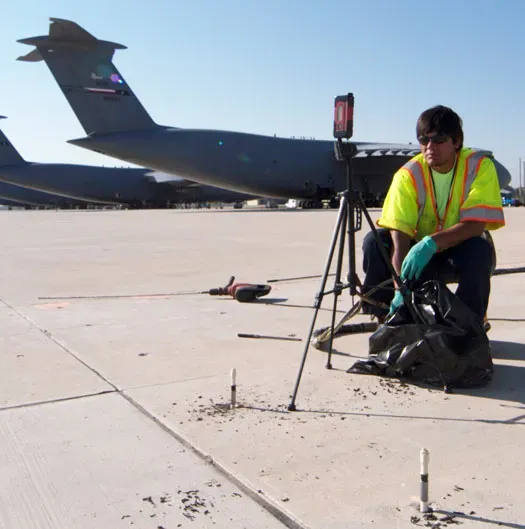