Polymer injection has long been hailed as a solution for rehabilitating roads, but one persistent issue has plagued the process: the leftover steel tubes embedded in the pavement. These tubes not only hinder the milling process necessary for asphalt recycling but also pose challenges to the structural integrity of the newly repaired roads.
The Problem with Typical Repair Methods
Traditionally, the thin-walled steel tubes used in polymer injection are either removed or left just below the surface after the injection process. However, this approach presents several drawbacks:
- Interference with Milling: Leaving the tubes at or slightly below grade results in milling machines cutting into them, contaminating the asphalt and preventing effective recycling.
- Potential Damage during Vibrating or Driving: Attempts to sink the tubes deeper post-injection risk damaging the newly formed bonds within the soil's geopolymer matrix, compromising the structural integrity of the repair.
- Structural Implications: Removing the tubes post-injection creates voids in the soil, leading to issues like moisture infiltration, sloughing, and weak soil layer reformation.
Introducing from URETEK: Countersinking with UDI®
URETEK has pioneered a game-changing approach to road rehabilitation with its patented UDI® system. Unlike traditional methods, UDI® countersinks all tubing before polymer injection, preserving crucial bonds within the soil's structure. Here's how it works:
- Pre-Driven Tubes: The UDI® process begins with tubes pre-driven 6” to 10” below the surface.
- Polymer Injection: Uretek's specialized polymer, URETEK 486 Star®, is then injected at the desired depth.
- Tube Retention: Tubes remain in place during asphalt recycling, eliminating the need for post-injection cutting or vibrating.
With Countersinking, UDI® Preserves Bonds That Other Methods Destroy
- Structural Integrity: With no cutting or vibrating required post-injection, the structural integrity of the tubes is preserved, ensuring a robust repair.
- Environmentally Friendly: UDI® supports contamination-free asphalt recycling, making it a greener solution for road rehabilitation.
- Safety Assurance: By eliminating the need for tube removal after injection, UDI® reduces safety risks associated with exposed tubing, ensuring a hazard-free work environment.
- Unrestricted Project Advancement: With no protrusions or limitations between shifts, project advancement is seamless and efficient.
- Optimized Injection Patterns: Uretek engineers injection patterns precisely to maintain volumetric control, preventing overuse and guaranteeing a minimal factor of safety.
- No Puncture Risk: Controlled traffic removal between shifts eliminates the risk of punctured tires or lost tubes, ensuring a safe work environment at all times.
URETEK DEEP INJECTION® (UDI)
Widely referenced within the industry, UDI® involves the injection of structural polymer into the base and sub-grade soils to increase their load-bearing capacity. The polymer is injected through small holes drilled directly through the pavement structure to a depth determined by site-specific analysis. Our URETEK 486 Star® material compact surrounding soils and apply a controlled pressure on targeted areas of the affected pavement above.
URETEK 486 STAR®
URETEK 486 Star® is developed to be the ideal solution for under-sealing, void filling, lifting of settled pavement, and stabilization. It is environmentally inert, non-toxic, and resists underground water erosion due to its industry-leading hydrophobic properties.
Want to dig deeper? Reach out to URETEK USA today to learn more about our innovative solutions in maintaining the integrity of commercial, residential, and infrastructure foundations. Together, let's build the future on solid foundations.
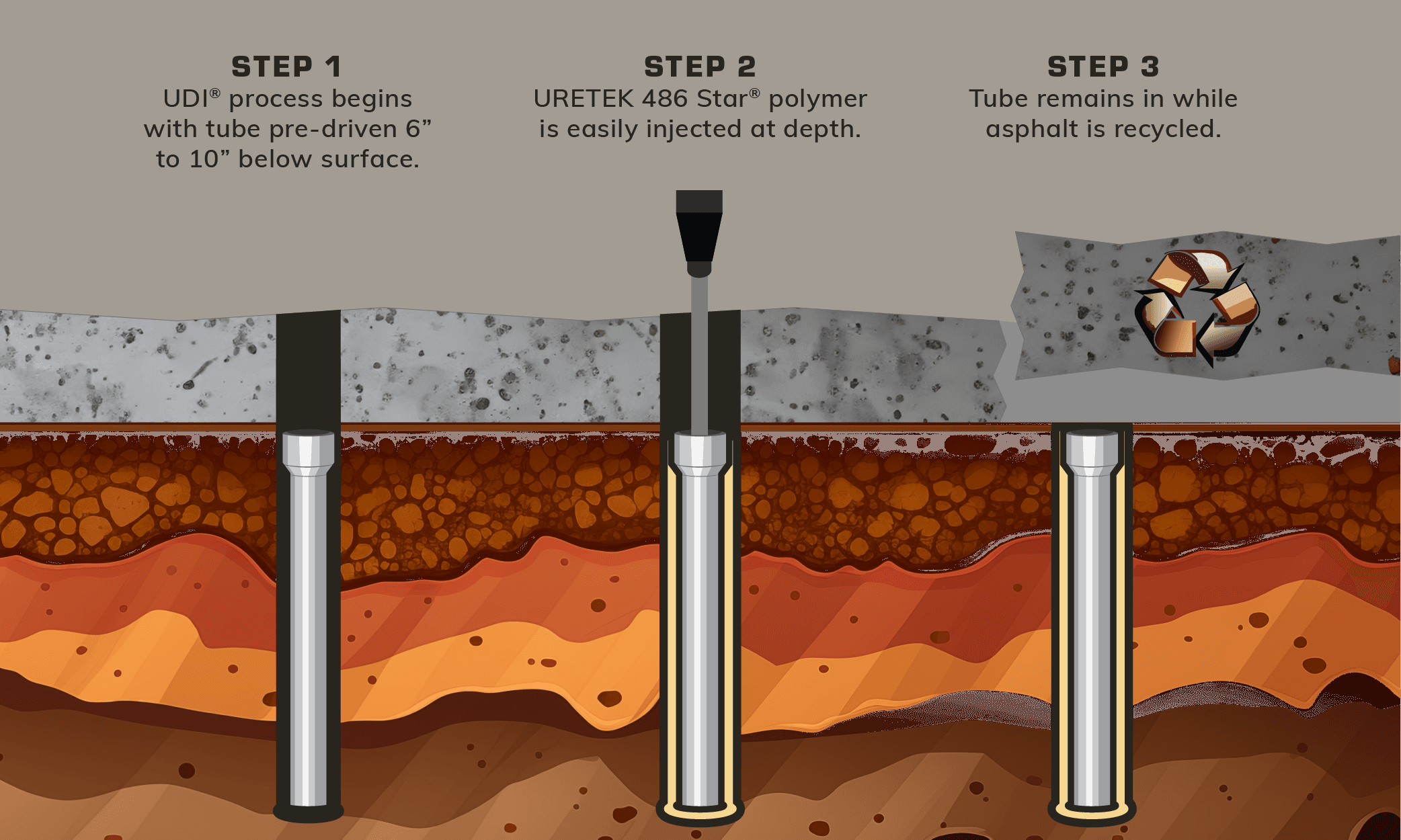